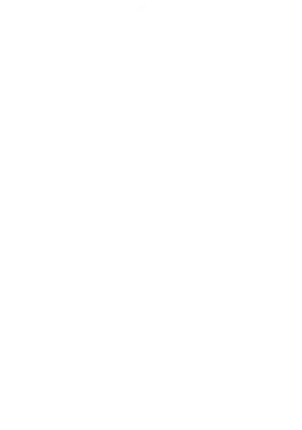
Space Planning in Industrial Buildings
In industrial logistics, space is not merely a physical boundary but a strategic resource. Effective space planning is essential for optimising warehouse operations, from storage to the movement of goods, ensuring that every square foot serves a purpose. In the UK, where industrial land is increasingly scarce and the demand for efficient logistics is rising due to e-commerce growth, intelligent use of space is more critical than ever. Whether designing a new build or optimising an existing structure, understanding how to best allocate and use space in industrial buildings is vital for ensuring operational efficiency, safety, and scalability.
Since 2005, Panattoni has delivered over 200 million square feet of institutional grade industrial logistics space across the UK and Europe, leading the way in defining and refining space planning for this critical infrastructure.
Maximising the flexibility of large-scale warehouses requires the resolution of several space planning issues. To find out more, read on.
What is ‘space planning’?
For those unfamiliar with the term, space planning is the art and science of organising and designing a building’s interior layout to ensure it is functional, efficient, and safe. In the context of industrial buildings like warehouses, it involves planning how different zones will be used – storage areas, operational zones, and transit pathways – and ensuring that the flow of goods and personnel is smooth and productive. This process involves a deep understanding of a building’s intended use, the types of products it will house, the equipment needed to handle these goods, and the workforce that will manage it all.
A well-planned warehouse layout can reduce time wasted in transit between zones, minimise accidents, and maximise the space available for storage without sacrificing operational flexibility. In addition, it helps future-proof the facility, allowing for expansions and modifications as the business evolves.
The warehouse planning process
In an industrial building, especially a warehouse, planning begins long before construction starts. The first step is to identify the core functions of the space. Will it serve as a distribution centre, a storage facility, or a manufacturing hub? What types of goods will be stored, and what are their specific requirements – temperature control, heavy-duty shelving, or fast access? The answers to these questions form the backbone of any space planning project.
Once the intended purpose is clear, architects and logistics experts collaborate to draft the internal layout. This often starts with a conceptual stage, using techniques such as bubble plans, where rough areas for different functions are mapped out. After that, more detailed drawings are created, incorporating precise measurements and layouts for racking systems, operational areas, and office spaces. In some cases, advanced digital tools like CAD (Computer-Aided Design) or BIM (Building Information Modelling) allow for 3D simulations of how goods and people will move through the space.
One of the key considerations in warehouse design is the flow of goods. The goal is to reduce the distance goods travel from storage to shipping and ensure that every product is easily accessible when needed. A well-thought-out layout will incorporate clear inbound and outbound routes, eliminating unnecessary detours or congestion points. Additionally, careful attention is paid to aisle widths, ensuring forklifts and pallet trucks can move freely without hindrance. Space optimisation must also consider future growth, ensuring the layout allows for easy expansion if demand increases.
The significance of column spacing
One critical but often overlooked aspect of space planning in industrial buildings is the layout of internal columns. Steel portal frames can facilitate huge spans, but the internal spacing of structural supports has a direct impact on the flexibility of a warehouse’s interior and its ability to accommodate various storage systems.
A wider column spacing allows for unobstructed movement within the warehouse, which is crucial when it comes to accommodating large-scale racking systems and facilitating the smooth operation of forklifts or automated material handling equipment. By reducing the number of columns per square metre, warehouses can store larger quantities of goods, and operational efficiency is enhanced as workers and machinery are not hindered by frequent structural interruptions.
In the UK, the standard column spacing for modern warehouses is typically 32 by 16 metres. This configuration is the industry benchmark because it strikes the right balance between structural integrity and usable floor space.
Maximising vertical space
In addition to lateral space planning, maximising vertical space is another essential strategy for increasing warehouse capacity. Vertical height offers additional volume for storage and improves the overall cubic efficiency of a building.
Haunch height
One key factor in this vertical strategy is the clear haunch height, which refers to the unobstructed vertical space from the floor to the lowest point of the roof structure – where beams or rafters typically sit.
The clear haunch height is critical in determining how many levels of racking can be installed within the warehouse. The higher the haunch, the more tiers of goods can be stored vertically, dramatically increasing the available storage volume without expanding the building’s footprint. Most modern UK warehouses are designed with a clear haunch height of 12 to 18 metres, allowing for efficient stacking of goods up to three or four levels of racking.
Hanging utilities
However, it’s not just about cramming goods into every available corner. The clear height also needs to accommodate overhead utilities like lighting, fire suppression systems, and HVAC equipment. These elements are typically suspended above the clear haunch height, ensuring they do not interfere with the warehouse’s racking systems or operational zones. Proper space planning in this regard ensures that the full vertical potential of a warehouse can be realised without sacrificing safety or accessibility.
Mezzanine floors
One way to further capitalise on vertical height is through the installation of mezzanine floors. These secondary levels, usually constructed halfway up the height of the building, effectively double the usable floor area without expanding the warehouse’s footprint. Mezzanine floors are ideal for slow-moving goods, office space, or additional packing zones. In cases where full vertical stacking is not possible – perhaps due to irregularly shaped goods or specific operational requirements – a mezzanine provides an elegant solution for optimising space.
For businesses experiencing rapid growth, mezzanine floors also offer a flexible and cost-effective way to expand without the need for new construction. As with racking, however, proper space planning is required to ensure that mezzanine floors do not obstruct the flow of goods or interfere with the building’s structural integrity. When planned correctly, mezzanine floors can provide significant operational benefits while ensuring the warehouse remains adaptable to future needs.
The importance of fit out
Once the shell of the building is constructed, the next phase is the fit out. This process involves installing all the necessary equipment, from racking and shelving to lighting, HVAC systems, and safety features like fire suppression. The fit-out stage also includes integrating the warehouse management system (WMS), which provides real-time data on stock levels, locations, and movement.
For many businesses, sustainability is a key consideration during the fit out. The use of energy-efficient lighting, eco-friendly building materials, and renewable energy sources can reduce the environmental impact of the facility while lowering operational costs in the long run.
Types of warehouse racking
Racking systems are a fundamental part of warehouse space planning, enabling efficient storage of goods and helping to maximise the use of available vertical and horizontal space. Various types of racking systems exist, each tailored to different storage needs.
Standard pallet racking
The most common is standard pallet racking, which is ideal for light, medium, and heavy loads. It allows for easy access to all pallets and can accommodate storage heights of up to 30 meters. Standard racking is sized for storing UK 1200 x 1000mm pallets.
Narrow and very narrow aisle racking
Narrow aisle (NA) and very narrow aisle (VNA) racking is another popular choice in environments where floor space is limited but vertical space is abundant. This system compresses the width of aisles to maximise storage capacity, increasing storage capacity by up to 40-50% when compared to conventional aisle widths. It requires specialised handling equipment due to the reduced manoeuvring space.
Drive-in racking
For companies dealing with bulk products of the same type, drive-in racking is a highly efficient solution. Instead of using individual aisles for each pallet, this system allows forklifts to drive directly into racks stacked several pallets deep, eliminating the need for dedicated aisles. This type of racking maximises storage density but is best suited for large quantities of identical goods.
Cantilever racking
Cantilever racking is another specialised system designed for storing long, bulky items such as timber, steel pipes, or metal beams. Instead of traditional shelves, cantilever racks use arms that extend out from a central spine, allowing easy storage and retrieval of lengthy goods.
Carton flow racking
For businesses that rely on rapid picking and packing operations, carton flow racking offers a gravity-fed system that moves products to the front of the shelf when one is removed. This first-in, first-out (FIFO) system improves picking speeds and reduces labour time, making it ideal for fast-moving goods.
Panattoni UK: delivering flexible warehouse space
In today’s fast-moving logistics environment, maximising both horizontal and vertical space is a priority for businesses looking to boost efficiency and reduce costs. Panattoni UK has positioned itself as a leader in the industrial warehouse sector by designing buildings that not only meet current industry standards but also anticipate the future needs of growing businesses.
Panattoni’s warehouses, such as their industrial units in Sheffield, are designed with a long-term vision in mind. Their specifications incorporate features like standardised column spacing and high clear haunch heights to provide maximum adaptability.
By offering a balance of structural robustness and operational flexibility, Panattoni ensures its warehouses can accommodate various racking systems, mezzanine floors, and other essential equipment without compromising efficiency. These features reflect the company’s deep understanding of space planning and its commitment to delivering industrial spaces that are as functional as they are future proof.
Conclusion
The importance of space planning in industrial warehouses cannot be overstated. From carefully considered column spacing to the strategic use of vertical space through high clear haunch heights and mezzanine floors, every element plays a critical role in ensuring that a warehouse can operate efficiently and adapt to future demands.
Panattoni UK stands at the forefront of this industry, offering expertly designed warehouses that meet the challenges of today while providing flexibility for tomorrow. By focusing on intelligent space planning, Panattoni delivers the type of industrial spaces that are essential for businesses looking to thrive in a competitive market.